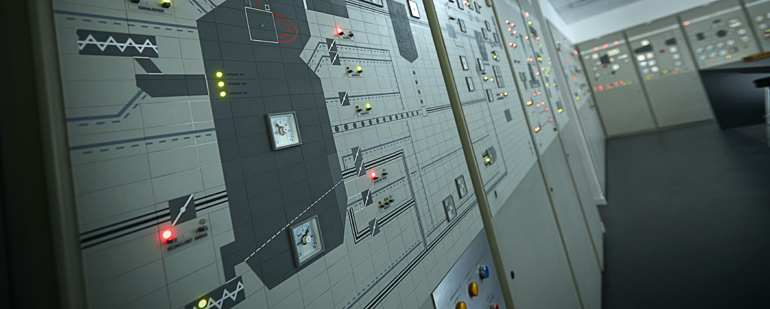
(Case 2, Annual Review 2018)
Missing daylight combined with nuisances from vibrations and noise formed a poor working day for the boilermen, in particular in the 24-hour manned control room at Køge CHP Plant.
Immediately below the control room you find the reason for the poor working environment – i.e. the two large pumps which supply the boiler with feed water. The two pumps are filled with rotating noisy parts which vibrate constantly. The pumps convert large amounts of energy which are transmitted to the building as low-frequency vibrations.
Behind his back
It was obvious from the workplace assessment from 2015 that the working environment was not at its peak. Sometimes the vibrations resulted in trembling keyboard and visible coffee circles in the coffee cup.
As they gradually realised how serious the problems were, the employees moreover started moving out of the room whenever possible. For good reasons, the boilerman could not leave the desk though.
Another inconvenient organisation was that the engineer on duty by the desk experienced that his col-leagues walked behind his back. They literally did that when they passed his seat.
Moreover, the old control room, which was originally built in 1985, showed traces of hasty solutions as to the number of workplaces. Since 2012, Køge CHP Plant has grown from 12 to 21 employees. One of the reasons is that people control and carry out work themselves which was previously managed by ex-ternal suppliers.
Last but not least, the legislation - and in particular the daylight requirements - have changed when it comes to permanent workplaces.
The floating room
Ten buckets of paint were not enough - changes were required...
The first step was to get a more detailed identification of the problems. Professional technicians were gauging and making analyses which left no doubt that the limits with regard to vibrations and noise from the two feed water pumps were exceeded.
Could the inconveniences be reduced by reducing the vibrations by the source? Unfortunately not. It was tried several times - without any luck.
Therefore, the only solution was to rebuild the control room at Køge CHP Plant with the following clearly defined objectives:
- create daylight
- resist noise, vibrations and improve the acoustics
- create better conditions for efficiency, concentration and cooperation
The solution ended up being a reconstruction where the control room was turned into a “cell” resting on different types of soft and flexible rubber. The old nuisances no longer affect the new floating room as the vibrations will be absorbed by rubber devices and the noise is reduced by a heavier mass in the walls and floor. The model with a floating room is twice as expensive as a standard office building but it was the only possible solution.
One thing remained the same: Floor heating from the warm pumps below.
Transparency
In connection with big changes, should the project management consider (read more about this in the side story) whether the target group is ready for the project? In this case, the answer was a loud and clear YES. Besides the straining physical working environment, the employees were met by a grey, dull environment every day. The function as an engineer is manned 24 hours a day, however, in principle the engineer could not tell whether it was day or night. It was like working in a submarine where it is hard to tell if the sun has been shining today.
Besides cutting a hole in the building to let the daylight in, VEKS prioritised together with the architect to position the guard in the middle of the room and that the 130 m2 large joint office should be open. The physical transparency through the entire open-plan office was solved by placing two glass walls on each side of the engineer’s desks.
The new control room also accommodates ten workplaces and a conference room besides the guard’s place.
A secondary aim when rebuilding the control room was to obtain a better integration of the employees. Improved physical settings for gatherings in the department among Køge CHP Plant’s three teams. These teams are an offshoot of VEKS’ reorganisation during the late summer of 2017.
Process
The project was offered as general contract where there was no prequalification due to the size of the amount of approx. two million. A screening of the market resulted in offers from three construction firms based on tender material and specification of requirements. A local construction firm with the lowest price won the assignment which was solved in a satisfying, flexible way without noticeable extra bills and on time.
What we can do, we do ourselves. Therefore, VEKS’ own employees have moved and built the new moni-toring Scala-system, disassembled the old electrical system, etc.
No surprises requiring radical adjustments turned up on the way. However, it turned out that the room was larger than the one illustrated in the drawings. However, the four extra square metres could be ab-sorbed in the existing budget without striking a blow.
The organisation behind
In the reconstruction phase, the steering committee was invited to a meeting whenever it was required - approx. every other month. The group’s job was primarily to decide on essential general decisions. In short, time, money and critical deviations. In addition, the project has a reference group which consisted of professionally qualified employee who had to use the control room. The reference group decided on the more practical aspects in the project, such as the architect's suggestion to furniture, colours, lighting control and lighting groups, screening between the ten workplaces, etc.
Naturally, the reconstruction was also a constant item on the agenda at the monthly departmental meetings among all the colleagues at Køge CHP Plant. And not all wishes could be fulfilled: The recon-struction should not be a “golden handle project” (in Danish “guldhåndtagsprojekt”) - working environment problems were to be eliminated but not by way of extravagant solutions. For instance, a music system which was a bit too fancy was cut away on the way.
Joy and credit
Is the mission accomplished then?
The final control room will be ready in the late winter of 2019. The project will be followed up by a work-place assessment after two months. Perhaps it needs some adjustments with regard to lighting control and heating system? Does it require some kind of adaptation to work in an open-plan office?
However, the immediate report from the employees has not diverged. High marks to all the new working conditions and settings. Perhaps it is not so difficult when the starting point was an unreasonable work-ing environment and some old trash...
The new control room stays the course - until 2040 which is so far the expected useful life of Køge CHP Plant.