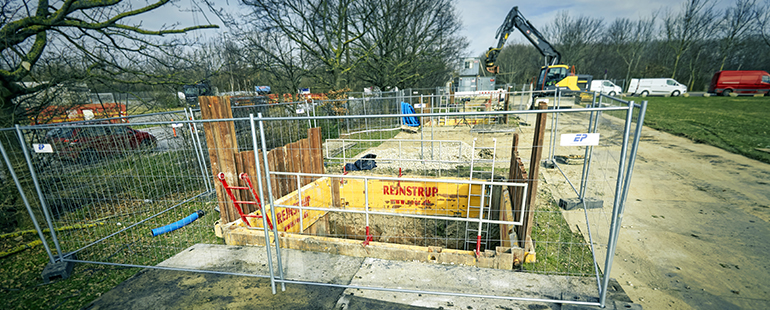
Case 2, VEKS' Annual Review 2021
Time has an impact on everything. VEKS’ system also requires increasing maintenance to preserve the values and guarantee high personal security - without supply failure.
Therefore, it is necessary to replace joints and re-stablish defect monitoring wires in several sections of the transmission system. And the target is? To ensure the district heating supply to VEKS’ customers.
Prior to this, feasibility studies have objectively and rationally prepared the strategy to where and when the renovation of joints and alarm wires should start.
Furthermore, the photo shoot of the year offers both an overview and shows details of this comprehensive maintenance project.
Joints – before and today
Everything is carried out according to a carefully prepared timetable where the existing joints are disassembled before every digging. After this, new alarm wires are drilled through the insulation foam into the district heating pipe and forward until the next joint and finally, the new joints are assembled.
The oldest pipes in the VEKS system were installed in 1987. 35 years is no age when it comes to media pipes which are the steel pipes in which the district heating water flows. In this closed system, efficient water treatment has ensured top quality and the pipes appear without any indication of wear. No, the problem is the 35 years old joints which have clear signs of wear. If a joint is not tight, water can penetrate the insulation which will thus be destroyed. There are three welding jobs per joint and the weak point typically turns out to be the actual welding.
At selected sections, a pilot project within Asset Management has analysed the joints and at the same time ranked them according to costs, frequency, impact, and risks. Force Technology has implemented comprehensive status assessments of selected joints. For instance, initial cracking and decay in joints and plastic caps occur.
Why does the joints not last longer? Shoddy job of the past, perhaps? Well, it is probably more about the development of material and methods where the specification of requirements are higher today when it comes to the joint method but also the introduction of new procedures and quality requirements to e.g. welding. Moreover, the plasticity limits have been changed which determine how much the mate-rial can be bended without being damaged.
Apart from higher quality requirements and standards, conclusive evidence is also required today; both when it comes to material and procedures. The documentation contributes to fulfilling VEKS’ goals of obtaining uniformity in ALL welding jobs.
Monitoring at several levels
All VEKS’ transmission pipes (forward and return) have monitoring systems installed by way of alarm wires and detectors. The monitoring systems control the transmission system and will immediately regis-ter – live – deviations such as pipe fractures, penetrating water, and alarm wire ruptures. If the alarm wire detects water, an alarm will promptly be sent to the operations centre.
With the alarm system, it is possible to react at the right time on a damage which is about to develop further. Hereby, you avoid expensive, acute digging-up and shut-downs.
New alarm wires
Therefore, the other important element in this servicing projects is to recreate alarm wires.
At several sections, a corrosion has developed in the alarm wires in the insulation foam surrounding the steel pipes
The alarm wires function as a leakage monitoring which can detect admission of humidity to the insula-tion foam which lies between the media pipe (with the district heating water) and the exterior jacketed pipe. It is important to avoid critical point damages from external dampness and water – e.g. from a damaged joint or if an external contractor digs into VEKS’ pipe system.
With alarm wires, you have the optimal solutions from a quality point of view as you have constant monitoring sending valid data – live.
The early wires are re-established – and thus the original complete alarm monitoring – by, in practical terms, drilling small new tunnels through the foam. When the drill is pulled back, four wires are drawn into each pipe at the same time. Two of the alarm wires are blank uninsulated copper wires which func-tion as moist detectors in the pipe’s entire length. The other two new extra wires are insulated in the pipe – but uninsulated in the joint – where they function as extra detectors.
Other monitoring
However, VEKS has by no means lost control of the system without the alarm wires.
Monitoring and detection of moist can also take place manually by the alarm technicians measuring the system through VEKS’ leak boxes which are placed 500-1,000 metres apart. Thereby, the technicians can detect damages and avoid critical leaks.
If the above measurement does not offer an optimal picture of the pipe system’s condition, VEKS also make use of drones to detect potential leaks. Through an infra-red camera, the drones monitor the sys-tem manually. However this type of monitoring can only be used when it is very cold as VEKS’ pipes lie relatively deep under the earth surface. Typically, VEKS has drones in action during the winter.
Prioritised working environment
The work is organised like beads on a string. Two gangs consisting of six workers work continuously in six excavations at a time – in each end of the section.
The work progresses positively, sometimes even ahead of schedule. It is, among other things, the result of new procedures. The firmly built crew is hired from external contractors, and the crew has established great routines and expertise within this special maintenance work.
For each hole there are two joints on the supply and return pipe and the cadence is 12 joints a week. In between the renovation of the joints, alarm wires will be re-established, as described above.
Today, in all the excavated shafts, prefabricated shoring boxes are used which is a steel construction in square standard sizes of 4-5 metres with a height of one metre. Below the shoring box, there are stand-ard bung at the depth of six metres.
The standard boxes offer protection against skidding and offer extra security and safety when working. The boxes have made the work more efficient and boosted the actual assembly of joints and alarm wires.
VEKS often performs safety inspections at the workplace to create the right settings for a healthy work environment, etc. The work environment coordinator is considered an asset at the workplace and is often sent for “voluntarily” by the crew members who want advice and instructions on how to solve tasks in a safe and healthy manner.
Work done...
In practice, the renovation of joints and alarm wires are carried out according to a well-planned time schedule and it runs very well! The progress is continuous, the project is under budget and the cadence is increased. Naturally, the speed is reduced a bit during winter where a long and challenging period of frost can delay or even stop the projects which are of course also closed during holiday periods.
Given the circumstances, the costs for renovating joints and alarm wires amounted to DKK 4-6 million per month in 2021.
Will we ever be finished? Yes, but not all of VEKS’ 17,000 joints are to be renovated...