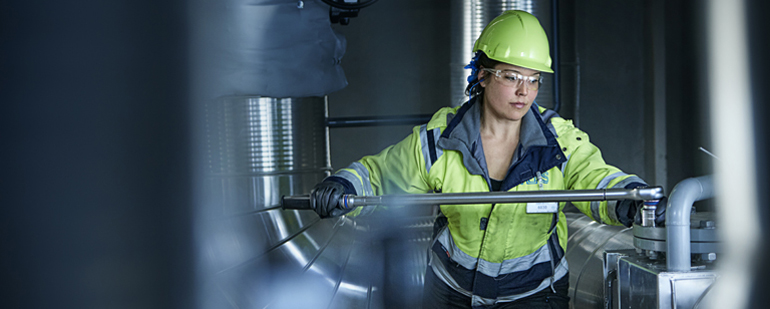
Case 1, VEKS' Annual Review 2017
On a national basis, expenses for work environment, illnesses and stress related to bad work environment annually amount to billions of Danish kroner. Therefore, there is a political focus on the area because society as well as the enterprises are strained. It also has vast human expenses - physical as well as psychological ones.
“We want to” opposite to “We have to”
Many enterprises are encouraged to give priority to a better work environment, if nothing else, for the money. It can be expensive to refrain from doing it.
In VEKS, work environment has always been a priority: “Because we want to – not “Because we have to”! This message permeates VEKS’ attitude and thus their actions. Therefore, the work environment is also expressed directly in one of VEKS’ strategy projects:” Optimise the environmental performance and work environment”.
QHSE? :Quality, health, safety, environment
Specifically, the intentions were converted into employing a person liable to the QHSE. Previously, the work environment tasks were outsourced to external consultants under the management of VEKS’ skilled work environment organisation. This construction with external competences was, however, neither durable nor up-to-date concurrently with the fact that VEKS has grown considerably in recent years, both when it comes to number of employees but also within the different business areas. At the same time, many legal requirements have been tightened up.
Applies to all
The goal is always to avoid work accidents. However, during 2018-2019 the target is also to have VEKS’ work environment measures ready for certification pursuant to the international standard ISO 45001. With the tools from a certification process VEKS professionalises their work partly by working systematically, partly by setting goals to improve the work environment.
But one thing is goals, certificates and documentation. Another thing is whether it gives an improved work environment? The answer is YES, if acted out by ensuring that the good intentions will be realised.
In VEKS, commitment, practical involvement and ownership are keywords when it comes to a healthy and safe work environment - for internal as well as external employees. VEKS cooperates on a daily basis with external employees who are associated with short as well as long temporary periods. The work environment and the safety instructions apply to all and therefore one of the first practical initiatives was to prepare a new environment and work environment folder with advice, references and requirements. Another specific initiative is an internal contact person course for a number of VEKS employees. Here, you find a brief description of what the responsibility and duties of a VEKS contact person includes in relation to a cooperation with external craftsmen, employees, service technician, etc. The goal is of course to always prevent work accidents.
New organisation for the work environment |
The selected work environment representatives reflect the work areas in VEKS’ new work environment organisation. The participants must represent according to a principle of subsidiarity as to their work and not their department. |
A participant from the group of employees as well as the executives are selected from the following three areas: |
|
|
|
Instructions
In a work environment system, the instructions for particularly dangerous work are important basic elements. These instructions are prepared as measures and with special focus on making them simple and operational. Thereby, they avoid drowning in the many instructions which the employees must otherwise relate to.
In connection with large projects, the contact person will be briefed and served by the QHSE employee who also participates in the start-up meeting with the supplier. The latter is also responsible for preparing an APV – a risk assessment of the relevant pending work. When the project is initiated, the QHSE employees will check whether the recommendations and requirements of the APV assessment agree with the job carried out. If it is a matter of mess and negligence which does not agree with the agreement, the supplier can be rejected. And simply stop the work.
Attention
With a QHSE employee in the company, environment and work environment are proactively included in tasks and projects at an early stage. It is also about visibility - with more means.
The work with work environment and environment add great value to VEKS. An important admission which is often experienced in the entire company concurrently with the fact that the culture is developed So far, a very executional culture has often occurred in VEKS: “Let’s get started!” And thus, there will be a risk of starting without sufficient planning of the task. In other cases, specific work processes may neither be reviewed sufficiently in advance. However, things take time. The first step towards incorporating environment and work environment from the beginning is to get used to considering the measures as a service function rather than a necessary evil. At the same time, it is not only about wishes and intentions - considerations for the work environment are stated requirements from the VEKS management. Care must be exercised and precautions should be taken. This has resulted in the QHSE employees referring directly to the executive officers. Because without the backup of the management, it may be difficult for the QHSE employee to reach his/her goal of ensuring tasks, action plans, delegation of areas of responsibility to contact persons, etc.
Active participation
Besides education and training, work environment is very much about visibility: How do we “make work environment an integral part of our projects”? As mentioned before, the QHSE employee will be involved early in the projects by simply participating in the meetings where tasks/projects are coordinated and planned. By being a part of it from the beginning, the work environment can be incorporated as an asset - an advantage - for the whole project. An example is the annual recurring summer review of Køge CHP Plant where the plant is closed and goes through a service check. “Plan for safety and health” is a practical tool which the QHSE employee prepares during the winter/spring so the plan is ready to follow in practise when the plan is checked in the allocated 3-4 weeks during summer. And the planning is working as the relevant employees are involved: This is our plan.
Above all, the new initiatives should make sense to you. A work environment which is implemented in numerous plans and work routines is second nature. The biggest difference between the new internal QHSE function is that the systematism must be more explicit and simple which will also benefit the exchange of experience and learning across the organisation. And above all, people still need to consider: Take care of the environment, yourself - and other people!